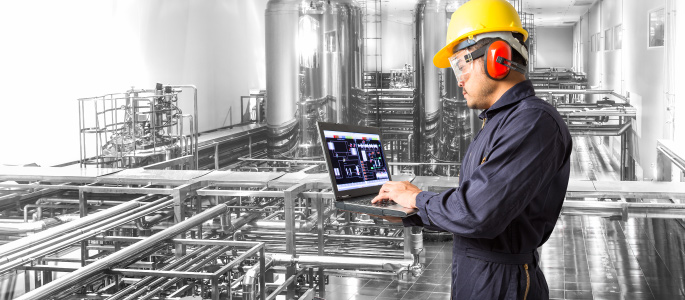
If you have landed on this blog page, you’re looking for guidance on choosing the right ERP software for your chemical manufacturing business. You are looking for an ERP solution that can outcast today’s challenges and make your operations simplified. This blog focuses on various best practices that can help you select the right one. So, read on –
Introduction
Implementing the right ERP software in your chemical organization can bring significant changes in the working and business processes of your company. Since it’s a one-time major investment that leaves a long-lasting impact on your business operations, key critical factors such as planning, selection of vendors, proper training, and knowledge transfer are considered before going for the final plunge.
A wrong decision can result in time, effort, and—more importantly—financial loss. Therefore, while choosing an ERP partner, analysis of current trends and an understanding of your demands should be taken into account. Speaking of Africa, manufacturers are in dire need to get technologies that can help them in automating their supply chain cycle.
Challenges faced by Chemical Manufacturing Industries
Chemical manufacturers today in Africa or worldwide face difficulties due to the shift in consumer preferences. The life cycles of products are getting shorter, yet item multiplication is still growing exponentially. Manufacturers need to maintain an ideal balance between inventory investments, customer service, and operating costs while remaining innovative if they want to beat their competitors.
Then there are complexities with respect to environments such as climate change, conservation, biodiversity, groundwater and soil contamination, natural resources, waste management, noise pollution, and air pollution. The industry heavily relies on partnerships, acquisitions, and mergers, because that’s how it expands operations in emerging and developing markets. And so, the biggest challenge is achieving successful post-merger integration and also, ensuring that post-merger operations are smooth.
Due to global developments, innovation as a core capability is the key differentiator and a key determinant of success, which is again a challenging task. And so, chemical makers are always searching for specialized, high-performance, long-lasting solutions that can eliminate all of the obstacles in one go.
If
You are facing these hurdles, or your current ERP software is inefficient, slows down, or does not blend in with the recent technological developments.
Then,
The time has come to take advantage of modernized and Next-Gen chemical ERP software.
But,
How to choose the software that best satisfies the requirements of your chemical business??
Selecting ERP Software for Chemical Industry necessitates a thorough understanding of the problems and requirements of the sector. A wide range of complex factors must be considered when thinking of solutions to manage personnel, compliance, and product needs.
So,
To make your ERP software selection easier and simpler, we have created an 8-steps guide to be followed that will help you in choosing and understanding a best-fit chemical ERP software. You can also Click here to know about the challenges that the chemical industry face.
Steps to Choose the Right ERP for Chemical Industry:
The following steps will guide you to make your choice and ensure that you gain the most value from your investment:
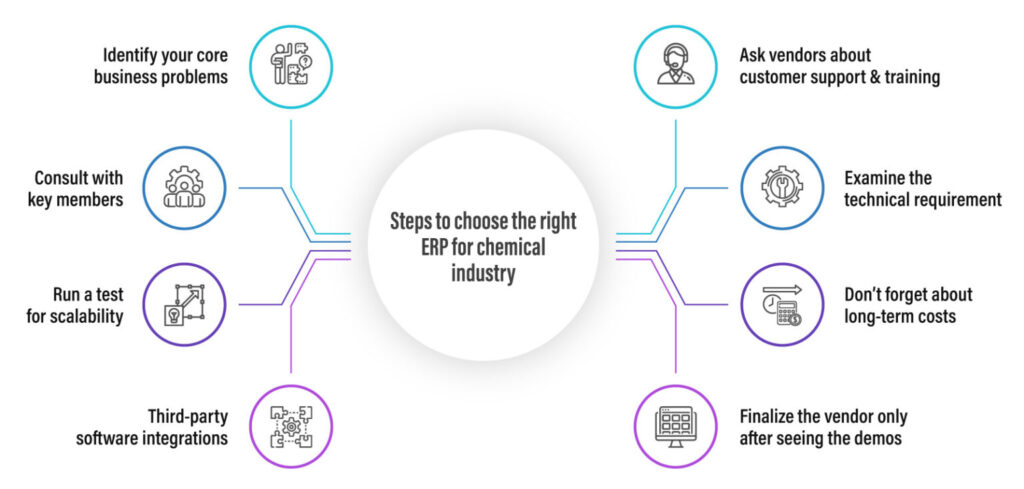
1. Identify your core business problems:
First, it’s important to review your company’s operational procedures. Check for documentation methods such as manual entry or double entry. Find out the business pitfalls and loose ends. Determine the time used for reporting. Find out what methods you use for adhering to compliance.
Write down all the problems you’ve experienced so far, and keep in mind that the unique requirements of the chemical industry cannot be met by generic ERP systems. Complete your investigation with a cost/budget benefit analysis after noting all the factors where problems are encountered.
2. Consult with key members:
ERP systems will be used throughout the organization; thus, it is important to consider the requirements and top objectives of each user. You can conduct a meeting and talk about the pain points and get their opinion to make everyone come on the same page. It may include key members such as:
- Company leader
- Development- Head
- Sales/Marketing -Head
- Warehousing, shipping, and receiving
- Production- Head
- Procurement and material handling – Head
- Financial and accounting personnel
- Data management and IT team
- Other parties in the supply chain
An ERP system should be analyzed from a usability perspective. Find out how the system will be used by each important team member, how long it will take to implement the solution, and how long it will take to become proficient with the new system.
3. Run a test for scalability:
When selecting an ERP for chemical industry, make sure that your requirement items in the check box are crossed off. You must take long-term requirements and corporate goals into consideration. Your ERP should be flexible enough to develop and grow with your company over time.
Though it’s becoming common for businesses to deploy ERP systems for future needs, but not all ERP systems offer the same degree of scalability and flexibility. It’s advisable to check for alternatives if you think your ERP might become obsolete in the next five to ten years. A bad fit ERP might hinder your business growth and will make you experience financial burdens.
4. Third-party software integrations:
After shortlisting some of the apt solutions that might satisfy your business requirement, you must consider the flexibility of the software integrating with the third-party software you are already using or planning to implement.
A lack or limit on integration can hinder your current processes or can force you the way you are doing business for years. You must select the ERP that blends in easily with the other applications and allows easy data migration.
5. Ask vendors about customer support & training:
Once your research is complete, speak with the ERP vendors about their employee training programs and support services. Keep in mind that implementation is only the beginning and that everything else follows, both benefits and challenges too. You will require ongoing support and help in addition to the initial launch for staff onboarding, training, system upgrades, and adjustments as your business grows or adapts to market changes. Ask them about the software’s usability and how simple it is for your team to use the modules.
6. Examine the technical requirement:
You must determine the kind of platform you’ll require—on-premises, cloud computing, or even hybrid. Ask your vendor about the infrastructure required to run ERP after discussing this topic with your IT team. Keep track of all the additional equipment required for ERP, such as internet access, the number of required users, mobile access, etc.
There is no one ideal hosting solution when it comes to infrastructure and equipment investments because what works for one company might not work for another. When considering your options to stay on track and within your budget, take the technical requirements and their accompanying expenses into account.
7. Don’t forget about long-term costs:
Although it’s essential to take into account your ERP’s upfront costs, you also need to consider the long-term expenses, just as with any key business investment. Chemical companies must not only cover the initial investment but also keep their ERP systems updated as their operations expand, upgrade their technology needs, and hire and train new staff.
Your ERP should be customized to suit your long-term company objectives. To continue achieving your goals, your system and vendor should be able to grow along with your procedures and operations.
8. Finalize the vendor only after seeing the demos:
Ask for demos of the software, understand each and every functionality in-depth, and how it will help with mapping your business operations. Don’t risk data security, backups and recovery instead make them a priority. Following this, you can choose the option that is most appropriate for your business operation once you have viewed the demos and comprehended the fundamentals.
Concluding Thoughts:
By thoroughly following the steps mentioned above, businesses can ensure the selection of efficient chemical ERP software. If you are Africa’s manufacturing company, contact us to know about an expert partner who can assist you with the selection and implementation of an ERP. Our in-house quality experts at BatchMaster Software will be pleased to help you.